National Tube Company: A Timeline
By Jason Togyer
The Beginning
1865: John H. and Harvey K. Flagler form Flagler & Co. in East Boston, Mass., to sell products made of iron.
1868-1869: Flaglers begin making their own iron at East Boston using one coal-fired furnace. One of their first products is cast-iron pipe.
1870: J.E. Converse invests in Flagler & Co., which changes its name to National Tube Works Co.
1871: Converse and the Flaglers decide to move closer to Pittsburgh to be near other iron and steel companies. They purchase the former Fulton-Bolman rope-making works, located on Walnut Street in McKeesport Borough.
Spring 1872: National Tube Works begins installing machine shops and pipe-making equipment in the old Fulton-Bolman rope-making factory.
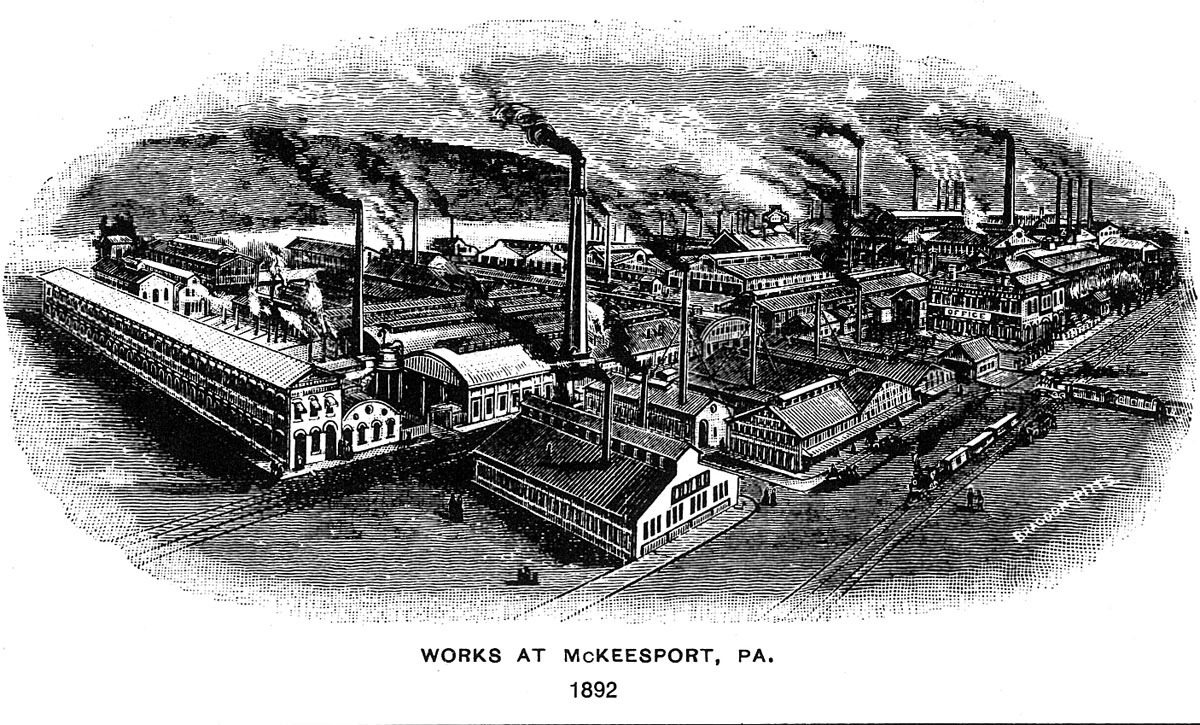
Advertisement
National Works opens in McKeesport
September 1872: National Works of National Tube Works Co. opens in McKeesport, with one welding furnace producing 2-inch diameter pipes for use in steam boilers. Pipes are made from sheets of iron that are rolled into tubes, and then welded. All iron is purchased from outside vendors.
April 9, 1873: Disaster strikes when the mill roof collapses. Sparks ignite gas mains and the National Works plant is destroyed. Plans for new building start the next day.
September 1873: New plant goes into operation with three furnaces.
January 1874: National Works receives contract for 10-inch diameter lap-welded pipe for a high-pressure water main in California. New machinery must be built that can bend heavy steel plates.
1875: New mill at National Works goes into operation. It is the longest and largest lap-welded pipe factory in the world, with the capacity to make 15-inch diameter pipes up to 20 feet long.
1878: National Works starts making its own iron, instead of purchasing it from outside. Construction begins on new rolling mills.
Fall 1879: New rolling mills go into service.
1885: Demand for pipe increases as natural gas use becomes widespread.
1886-1887: Two more lap-welding furnaces built.
1886: Butt-weld mill built.
1887: Another new lap-welding mill goes into operation which can make pipe up to 24-inches in diameter.
Steel making begins in McKeesport
1890: The Monongahela Furnace Co. is created with $1 million investment. It begins construction on a steel-making facility next to National Works. Monongahela Furnace will send almost all of its steel to National Works, to be turned into pipe.
1891: Borough of McKeesport becomes a city.
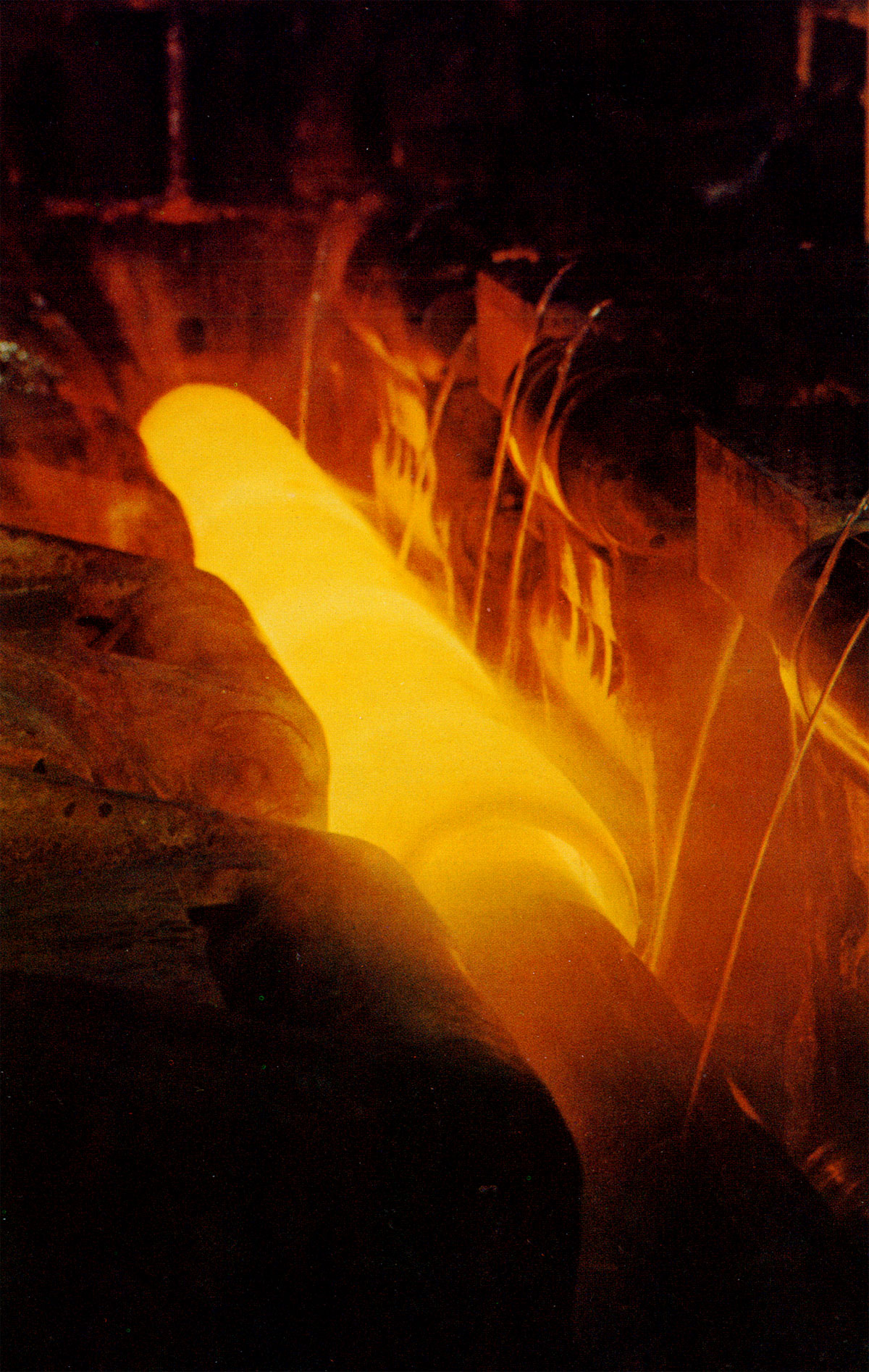
1892: National Works begins making seamless steel pipes (above), which do not require welding.
1897: First electrified machinery for manufacturing pipe is installed in the plant.
July 1, 1899: National Tube Works Co. merges with other companies in Pennsylvania, Delaware, Ohio, West Virginia and New York to form National Tube Co., with McKeesport's National Works as its main plant. The company controls about 70 percent of all steel pipe and tube made in the United States, ranging from sizes down to 1/4-inch in diameter, up to 30 inches in diameter.
Major expansion program begins
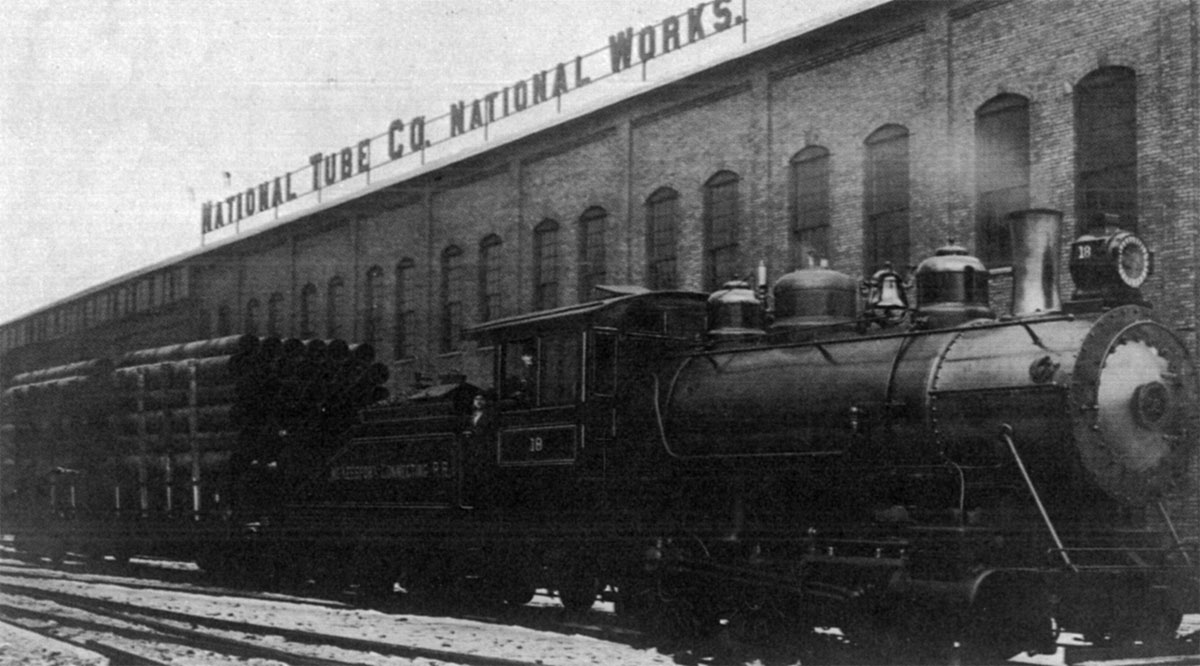
March 1901: National Tube Co. merges with U.S. Steel Corp.
1904: A major reconstruction and expansion of McKeesport's National Works begins.
1905: National Works produces 767,000 tons of steel in a single year, with pipe of all diameters stretching to a total length of 450 million feet.
1908: Six new butt-weld mills are built, capable of producing single pieces of pipe ranging from 22 feet long to 41 feet long, in diameters from 1/8-inch to 3 inches.
1909: 12 new lap-weld mills are built. These can produce pipes ranging from 4 to 24 inches in diameter, stretching up to 42 feet long. All of the original butt-weld and lap-weld furnaces are dismantled.
1912: National Works has largely taken over the entire McKeesport waterfront, along the Monongahela River, from the Riverton Bridge --- where the steel furnaces are located --- to Walnut Street, where the plant's office and machine shop are located.
1929: The Great Depression begins, reducing demand for steel and iron.
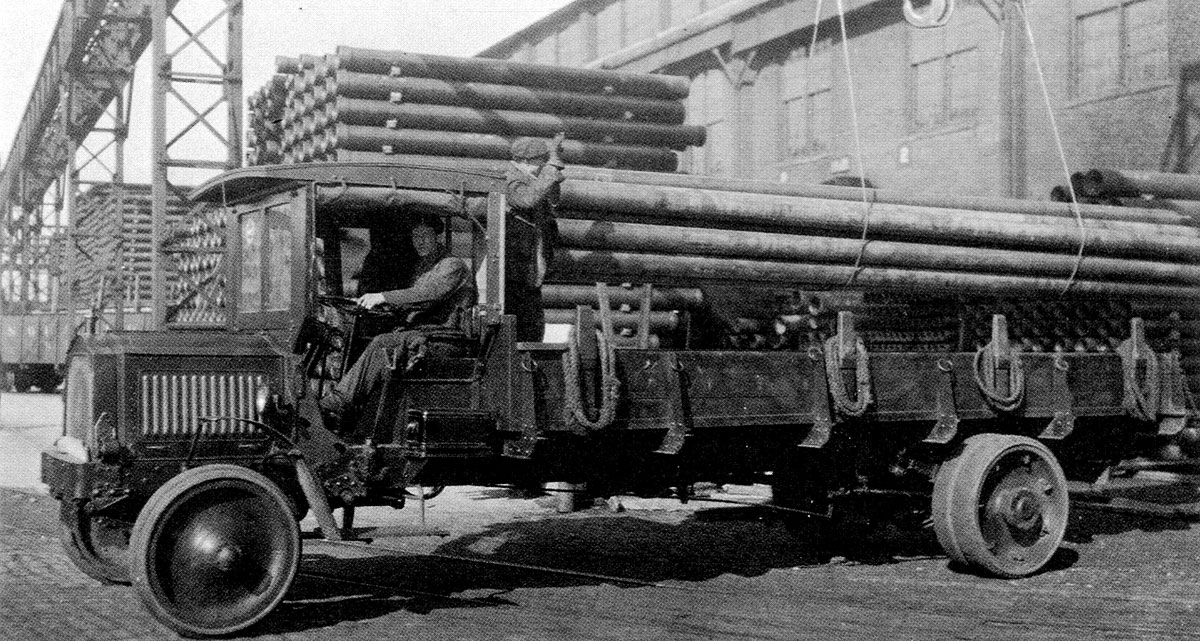
1930: New seamless pipe mills are opened, producing pipes up to 48 feet long, with diameters from 3.25 inches up to 24 inches. Three new Bessemer Converters are built; these produce steel from iron. A new gas pipeline connects National Works to the Clairton Coke Works. National Works now employs 8,800 workers. The nearby Duquesne Works of U.S. Steel has 9,000 workers.
1931: Three new 200-ton open hearth furnaces, used to turn iron into steel, are opened.
1934: National Works produces five different varieties of pipe and 964,000 tons of steel.
1940: The last remaining lap-weld mills at National Works are closed and dismantled. From now on, all National Works pipe is either seamless or butt-welded.
World War II peak production: 3.1 million tons
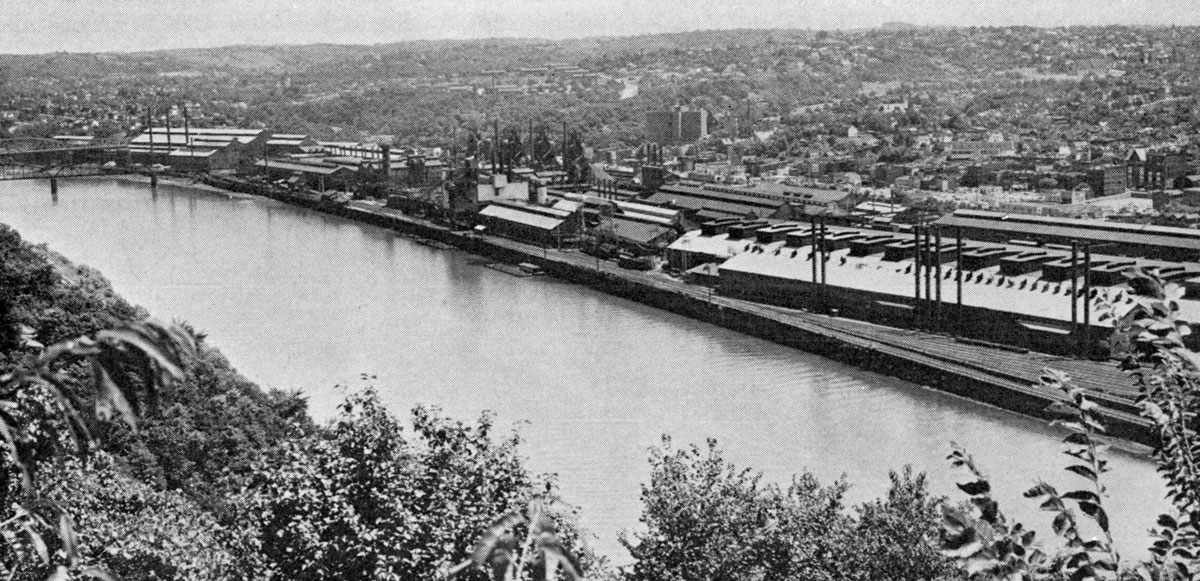
1941-1945: National Works converts to wartime production. At peak operation, National Works turns out 3.1 million tons of steel from its open hearth furnaces and Bessemer converters.
1946: National Works' remaining butt-weld pipe mills are dismantled.
1950: New electric-welding mill built for manufacturing thinner, lighter pipe ranging from 26 to 36 inches in diameter, in lengths up to 40 feet.
1960: Demolition begins in McKeesport's First Ward neighborhood --- houses, stores, churches and synagogues located where the Youghiogheny River flows into the Monongahela River, north of Lysle Boulevard. U.S. Steel has purchased about 1 million square feet of land for approximately $1 million (1960 dollars). A new electric-resistance weld mill is built on part of the land. The rest of the land is used for a new railroad yard to serve National Works.
1964: U.S. Steel Corporation reorganizes into four main business units. National Works falls under U.S. Steel's new Tubular Operations unit. U.S. Steel employs 6,300 people at National Works and at Christy Park Works, which is located on Walnut Street south of the 15th Avenue Bridge. Christy Park Works, covering 34 acres, produces bomb casings, gas cylinders, metal containers and other products from pipe and steel.
Blast furnaces closed
1966: Four blast furnaces at the plant are closed. Two reopen the following year, only to be closed again.
January 1969: National Works of U.S. Steel's Tubular Operations merges with Duquesne Works of U.S. Steel's Heavy Operations to form National-Duquesne Works.
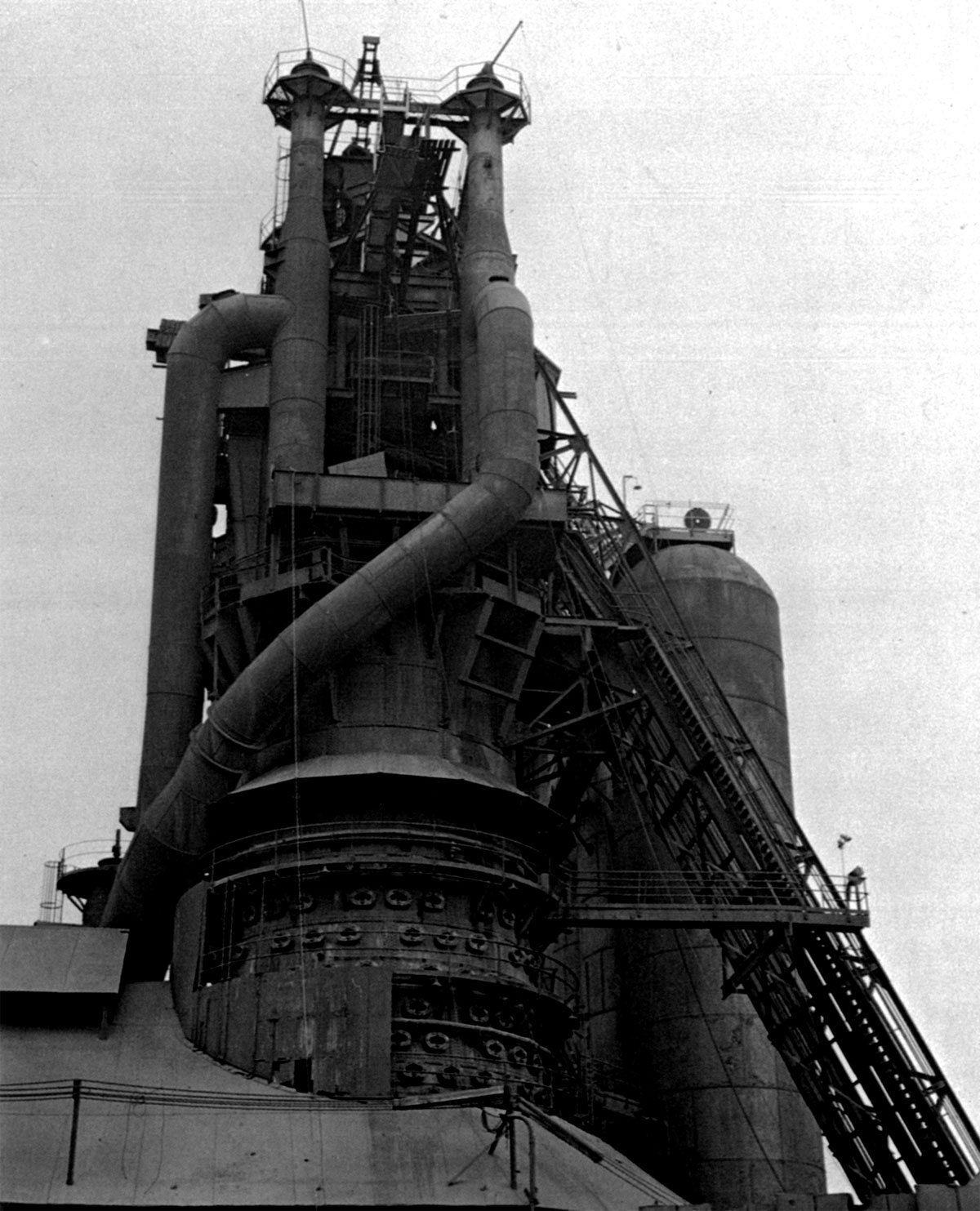
October 1970: National Plant's No. 1 blast furnace (above) is converted to produce ferromanganese, which is a key ingredient in high-quality alloy steels. National Plant managers hope that No. 1 furnace will soon be supplying most of U.S. Steel's need for ferromanganese across the country.
September 1972: National Plant celebrates its 100th anniversary.
March 1973: One of the blast furnaces at National Plant that was closed in 1966 is rebuilt by U.S. Steel and put back into operation at a cost of $3 million (1973 dollars).
October 1973: Syria and Egypt attack Israel. America delivers weapons and supplies to Israel. Arab nations respond by putting restrictions on exports of oil to the United States and raising the price of oil. The first oil crisis begins and energy shortages hit America.
Pipe demand increases during oil crisis
1974-1978: American oil companies respond to the Arab oil embargo by beginning to drill more oil and gas wells in Texas and Louisiana. Demand for steel pipe increases. About 4,500 people are employed at National Plant.
June 1981: Economists begin to warn of an "oil glut" caused by increased exploration and reduced demand. Oil prices fall rapidly.
July 1981: U.S. economy goes into recession.
September 1981: A new quench-and-temper line opens at National Plant. This line is supposed to be used to harden steel pipe to make it stronger. It will be U.S. Steel's last important investment at National Plant.
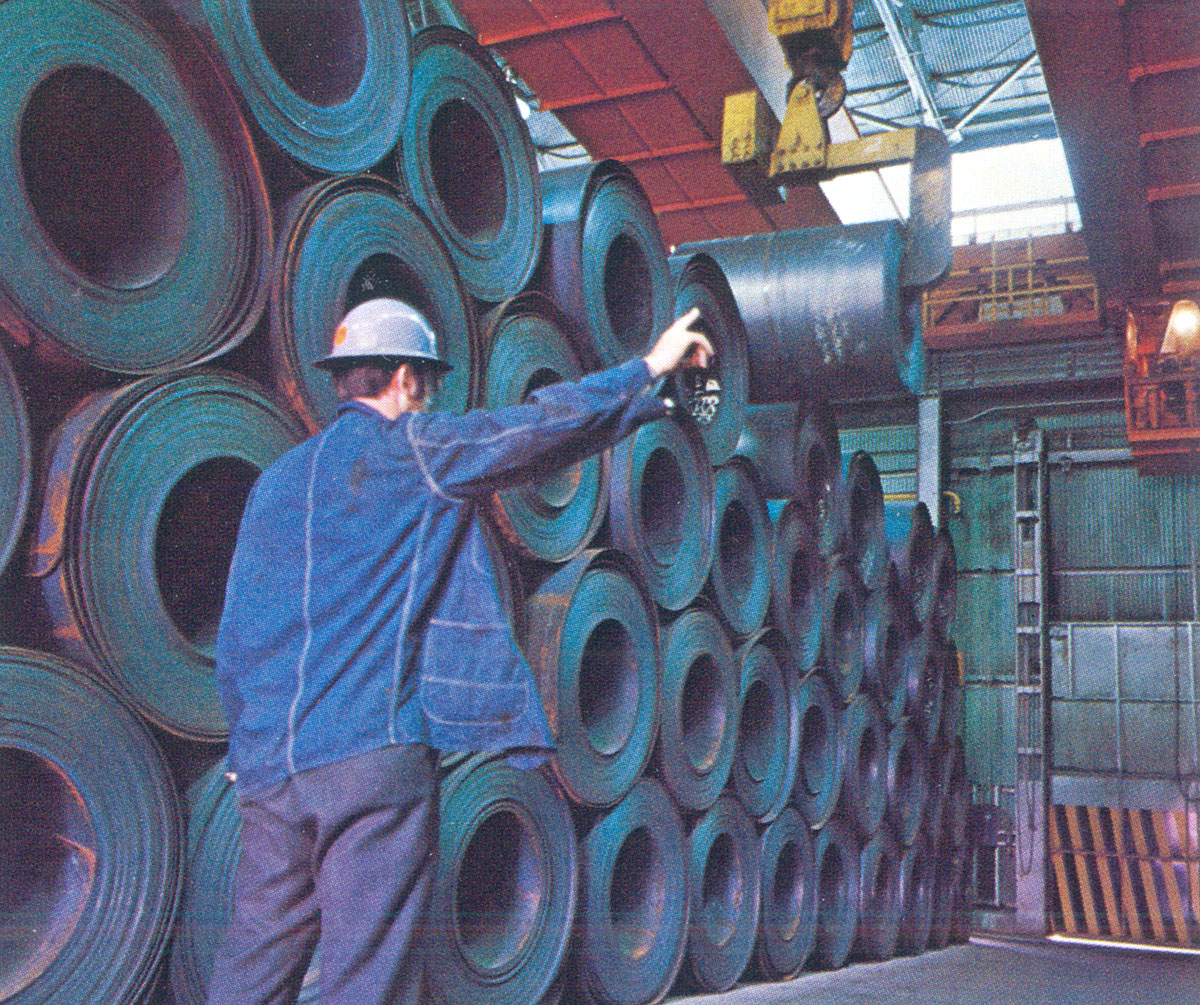
Advertising
Major layoffs begin
November 1981: As oil and gas companies cancel pipe orders and the recession gets worse, U.S. Steel lays off 6,200 steelworkers throughout the Mon Valley.
National Plant's blast furnaces are permanently closed.
But A.L. Voss, superintendent of National-Duquesne Works, tells a lunchtime audience at the Duquesne-West Mifflin Chamber of Commerce that the plant "is in a very good position" to resume full operations.
December 1981: U.S. Steel Corp. announces plans to purchase Marathon Oil Co. of Ohio for $6.3 billion.
January 1982: U.S. Steel's purchase of Marathon Oil is approved by the U.S. Supreme Court in January 1982.
The Marathon Oil purchase angers steelworkers, who complain that the $6.3 billion could have been used to modernize and keep steel plants open.
March 1982: 3,500 National Plant employees remain laid off. Vice President George H.W. Bush visits McKeesport and is picketed by laid-off steelworkers, who complain that President Reagan's anti-inflationary policies have deepened the recession.
April 1982: U.S. Steel's Mon Valley plants are shut down for four days because of reduced demand for products.
June 1982: Leaders of the United Steelworkers union agree to demands from U.S. Steel and other steel companies to reopen their contracts to cut wages and make other concessions.
May 1984: Employees who work at Duquesne Plant's famous "Dorothy Six" blast furnace receive "steel master" awards for beating all U.S. Steel production quotas. One day later, they are laid off.
Duquesne plant closed
June 1984: Only 1,000 workers remain at Duquesne Plant, which is making rolled steel and steel shapes. U.S. Steel announces that Duquesne's remaining mills will close and production will be shifted to a U.S. Steel plant in Lorain, Ohio
"Duquesne is clearly slated for shutdown," a U.S. Steel executive announces.
October 6, 1984: U.S. Steel announces plans to demolish most of the Duquesne Plant to clear way for an industrial park.
October 29, 1984: U.S. Steel announces plans to demolish the steel-making furnaces at National Plant --- covering about 40 acres, near the McKeesport-Duquesne Bridge -- to clear way for an industrial park.
December 1984: Steelworkers rally to save the "Dorothy Six" furnace and recruit volunteers to winterize the facility, in hopes that a buyer can be found to re-open the Duquesne Plant.
January 29, 1985: U.S. Steel Chairman David Roderick tells reporters that he finds it "doubtful" that Dorothy Six will ever re-open.
1985: National Plant remains open, employing about 350 people. Some work in the electric-resistance weld department, but others are kept busy finishing and testing pipe brought in from other facilities, including from overseas.
Demolition of the blast furnaces in McKeesport begins.
October 1986: Contract talks between U.S. Steel --- which has changed its name to USX Corp. --- and the United Steelworkers union break down and a strike is called. About 22,000 employees walk off the job. The strike lasts six months.
McKeesport plant to close
Feb. 4, 1987: The strike against USX ends, but 189 employees of National Plant arrive at work and are told their plant, as well as others in Utah and Texas, will remain closed indefinitely. The only people retained are those to perform maintenance and to ship leftover pipe to customers, and machinery to other USX facilities.
USX's Roderick tells reporters the outlook for National Plant is "extremely bleak."
Aug. 29, 1987: Only about 21 people remain employed at National Plant during the last day of operations.
December 1987: USX confirms that "several companies" have expressed interest in reopening the electric-resistance weld mill and "possibly other portions" of National Plant.
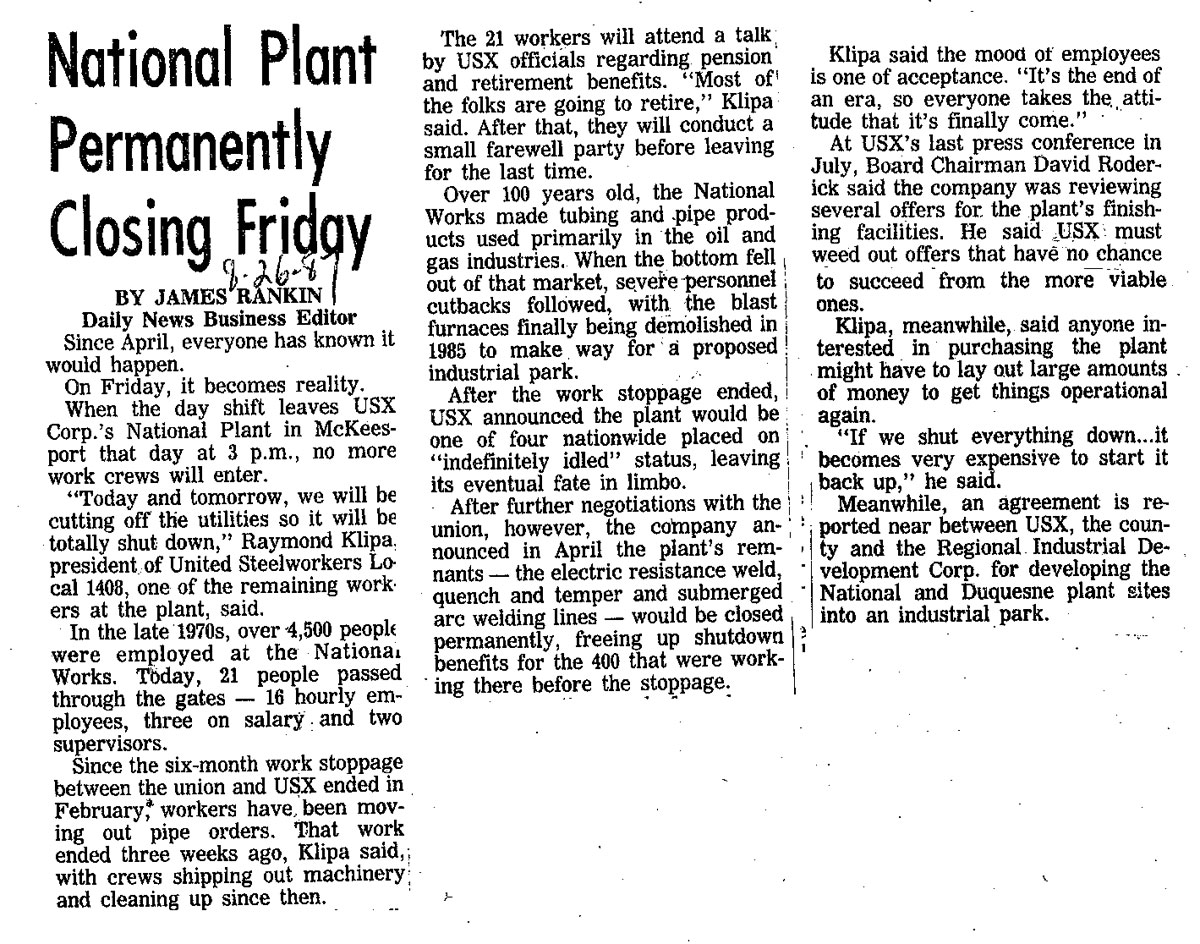
All research by Jason Togyer. © 2017 Tube City Community Media Inc. and Jason Togyer, all rights reserved.
---
This article is from tubecityonline.com/steel, the Steel Heritage section of Tube City Online, P.O. Box 94, McKeesport, PA 15134.
|